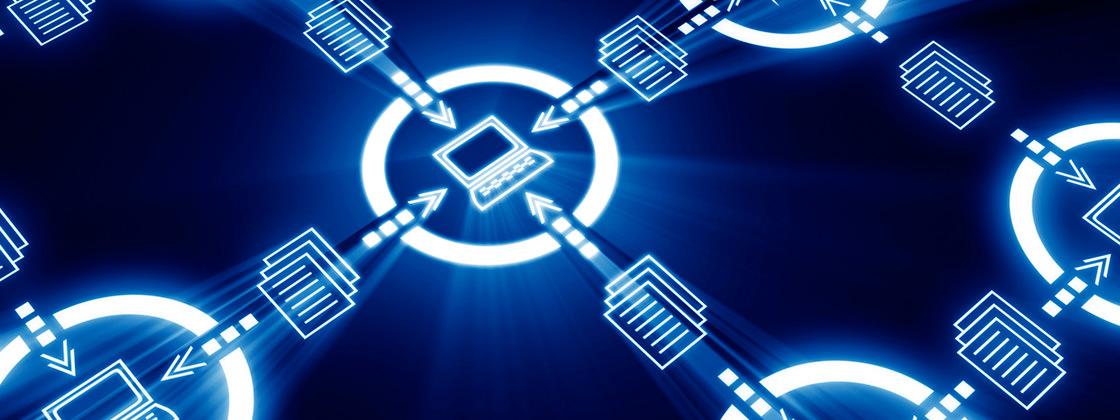
During the development and design of new products, numerous data such as technical drawings, parts lists or test results are generated. A major portion of such information is still needed in the further course of the product life cycle in relation to service, maintenance or continuous further development. With cc|product data management , the COSMO CONSULT group introduces a certified add-on onto the market that adds the functions required for this to the ERP system Microsoft Dynamics NAV.
Technical documents always ready
With the add-on module, companies can manage technical documents from areas such as mechanical engineering, electrical engineering and electronics company-wide based on consistent rules. Drawings and documents relevant to production, purchasing or service are provided automatically, depending on the situation, during the process. Also the drawing revision after product changes will be carried out independently by the software. The most important functions of cc|product data management include:
- the integrated drawing management,
- the revision management
- the consistent change management and the
- connection to more than 20 common CAD/PLM/PDM systems.
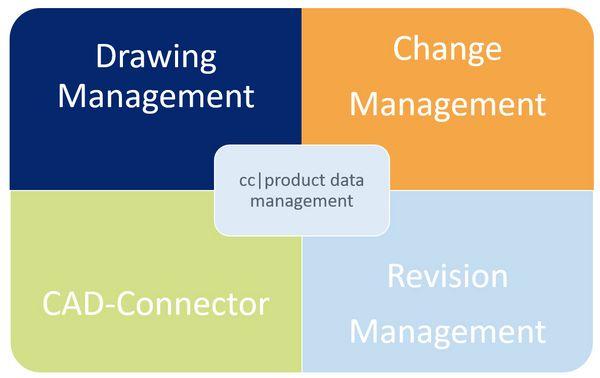
Efficient drawing management
Via drawing management, any number of drawings and drawing revisions can be managed. These can be flexibly assigned to items or parts lists and, consequently, allow for a higher transparency with a view to the subsequent data usage. Via status management, engineers are able to specifically include or exclude drawings or documents in or from the process.
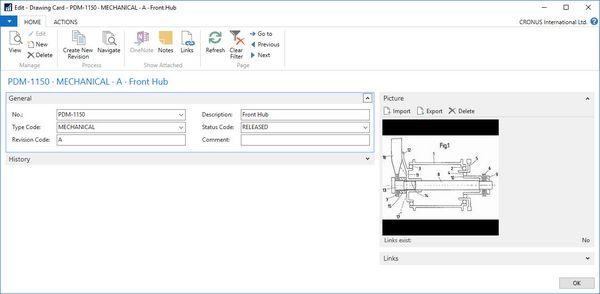
Reliable revision management
Revision management ensures the consistency of data in the case of changes. An important point is the usage check which determines the application area of the individual drawings. Based on this information, it will then be decided if the entire product structure, the assembly or only the individual part is to be revised.
Transparent change management
Through change management, cross-departmental processes can be controlled specifically. The change requests will be directly transferred to the design department. Detailed information about the type of change and the components affected are available. On this basis, the designer can then check the process and decide about product changes. Each product change is included into the company organization via a change order. In addition, a flexible task list defines the jobs of the departments involved. As a result, designers can recognize the current status of the changes at any time.
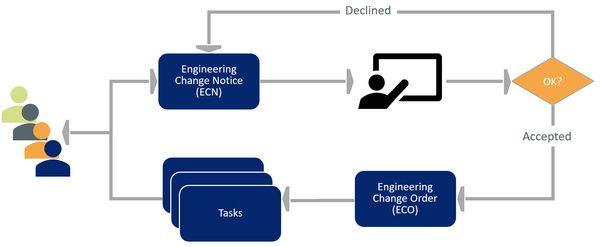
Compatible with CAD, PDM and PLM systems
Via the optional cc|product data management connector, common CAD, PDM and PLM systems can be connected with cc|product data management. The individual alignment of the industry solution with the respective operational requirements ensures that the data in the ERP system are always up-to-date. This means that, in addition to drawings, items and parts lists, also processes are harmonized between CAD and ERP systems.
If you would like more information about our new solution, please contact us.
Keywords
More similar news articles
Found what you were looking for?
Start your intelligent search now