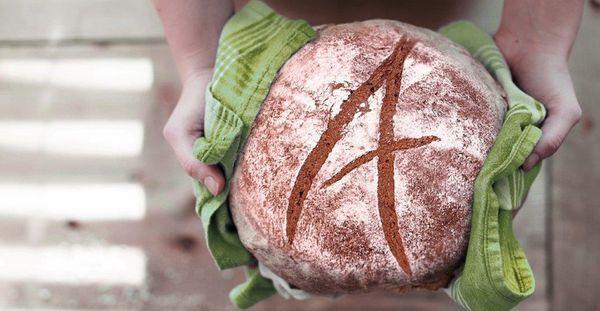
ARTiBack GmbH
Have you noticed? Something’s happening in the bread and roll baskets at discount stores and supermarkets. Where there used to be inconspicuous shelves of baked goods, we now see glass bakery shops. Instead of exclusively on low-cost products, the assortment is now wider than what you'd find at some bakeries. We’re seeing a trend towards high quality baked goods. One business that’s riding this wave is ARTiBack GmbH, founding in Halle, Germany, in 2016. The company’s name says it all: “art” stands for “artisan” and “i” is for “innovation.” The company relies on traditional ingredients like flour, water, salt and yeast, while additives like enzymes and emulsifiers are intentionally left out. Buyers of the frozen products include retail chains, wholesalers and caterers. When the company was founded, one of the biggest challenges was combining high standards of quality with the sector’s traditionally low profit margins. The solution was extensive automation in the production process and the use of modern IT technologies in order to control production, logistics and quality assurance.
Functionality was a crucial factor
As a growth-oriented company, they were looking for a business software that would respond flexibly to a growing number of employees and higher requirements over the long term. The idea of introducing a specialized industry software for large-scale bakeries was quickly rejected based on its limited investment reliability. “We didn't want to be dependent on a small vendor with an uncertain future,” explains Doreen Weber, IT Director at ARTiBack GmbH. Instead, the company opted to choose one of the biggest name ERP systems. Ultimately, Microsoft Dynamics NAV (now Microsoft Dynamics 365 Business Central) won out over SAP solutions. The task of implementing it went to software and consulting company COSMO CONSULT. “COSMO CONSULT was the only service provider capable of incorporating all the processes and functions in one system. That way, we had a lot fewer interfaces to manage.” In order to do this, Cosmo Consult enhanced the ERP software by adding the industry solution Processmanufacturing, the workflow management system Workflow and the EDI module, which allows for data exchange with food retailers in electronic data interchange (EDI) format. In addition, the Qualitymanagement software handles batch tracing, receiving and outgoing inspections or audit preparation, all of which are crucial in the industry.
Re-imagining processes
One of the advantages of introducing a new system is that there are no established work flows and structures. The project team was able to model business processes without having to consider existing habits or ways of thinking. The software standards, meanwhile, were already defined, and any deviations had to be justified. “Naturally, there were some adjustments to be made, but in the core areas like quality assurance, logistics and production, we basically work like any other business in the process industry. We take various raw materials according to the recipe and combine them to make a new product,” explains Doreen Weber.
The implementation was completed in several phases, parallel to the construction of the factory and the start of production. First to launch were the commercial departments like Finance and Assets Accounting. Once production work got started, Payroll, Production Planning and Control (PPC) and Logistics soon followed. The project team started by simulating production workflows and deliveries before the first actual order was put through the almost entirely digitalized process.
Efficiency from start to finish
Now, staff from the Goods Receiving Department registers the incoming raw materials and additives using mobile devices. Ingredients such as flour, water or yeast are then input into the production process by Microsoft Dynamics NAV according to each recipe. The only manual work to be done is the occasional addition of seeds or grains. The rest of the workflow, pre-baking times and cooling are also fully automated. Finally, the software submits the pick-up orders to the shipping company via EDI.
Some smaller adjustments also had to be made in Quality Assurance, since ARTiBack doesn’t only track batches but also individual pallets. For this purpose, the team gave the order structure a hierarchical grouping system. “If a batch has 200 pallets, each pallet gets its own tracking number,” explains Weber. In order not to interrupt the cooling chain, the goods are loaded onto the truck straight off the production line. This saves ARTiBack time, space and the effort of interim storage.
Stress-free system launch
Currently, the business software is installed at 20 workstations. In addition, there are two mobile scanners at Goods Receiving that exchange their data with Microsoft Dynamics NAV by means of the cc|mobile solutions add-on. The IT director is satisfied all around with the way the ERP project has gone. “We're working with lean processes. Operations can be posted or modified with little manual intervention. Another advantage is the transparency. We get comprehensive evaluations that let us quickly see what’s going on in every area of the company.” She also had good things to say about working with COSMO CONSULT. “The whole project went off without a hitch. In the end, the processes worked the way we intended. We also stayed within the budget. And when we saw that the simulations and test deliveries worked from the first try, that’s when we really knew we could relax,” Weber recalls.
Digitalization marches on
Following the system launch, ARTiBack first implemented a few minor process optimizations. Now, Weber wants to keep working through the bigger items on their wish list. Most of all, we’re interested in further digitalizing the workflows. “There’s still too much paper involved, especially in Quality Assurance. Another item is vendor evaluation, which is currently still done entirely in Excel. We want to equip our software with the functions we need as quickly as possible,” stresses Weber. Soon, we’ll be able to log working times and waste from mobile devices, which is going to cut down on management work. They’re also already testing out Microsoft Power BI – in the future, this software will provide workers with current business figures, displayed on easy-to-read dashboards.
More COSMO References
Be part of our COSMOs
Expand your COSMOs and register in our customer portal for exclusive benefits & services
#myCOSMO
Found what you were looking for?
Start your intelligent search now