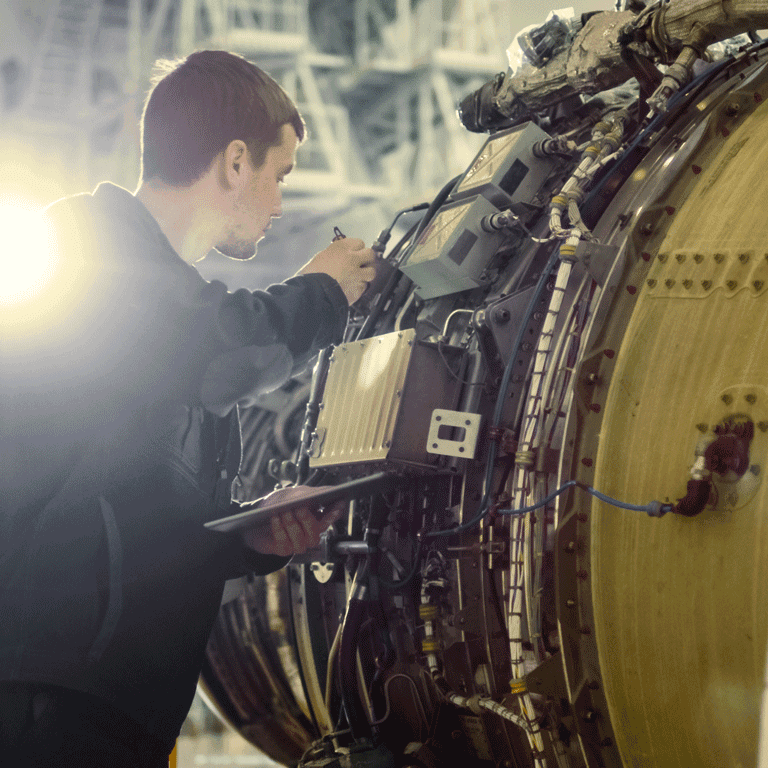
How to ensure the maintenance of production facilities is one of the important strategic business decisions. A Computerized Maintenance Management System (CMMS) can transfer this strategy to the digital world and implement it in operational practice. Such a solution should ideally be fully integrated into the enterprise software.
Maintenance Is a Question of Strategy
A company’s production and added value are at risk if critical equipment or machinery cannot be repaired or breaks down. Downtime for repair or replacement then quickly becomes a costly problem. How companies reduce or—better still—avoid the extent of this disruption completely depends largely on the maintenance management strategy they choose. A digital solution is the best approach here. This means your team can continuously monitor production, plan and carry out regular maintenance, and repair defective machines as quickly as possible.
Different Maintenance Strategies
Preventive maintenance avoids malfunctions such as machine breakdowns or unplanned downtime—and is typically based on scheduling or the technical condition of a production plant. Digitalization now allows data-based, predictive planning of maintenance or servicing. This involves systems with artificial intelligence and sensors taking over the continuous inspection of central components and consumption. They calculate maintenance dates and suggest improvements to the machines based on the data analyzed.
In contrast, corrective maintenance takes a purely reactive approach: machines are not serviced or replaced until they actually fail. Corrective maintenance can make perfect sense for organizations or factories with tight budgets or low security risks.
The Advantages of Digital Maintenance
In most cases, companies use a combination of strategies. However, it is important for the four basic steps of maintenance to be mapped in the IT system: inspection, maintenance, repair, improvements.
The IT system creates digital work order plans for this purpose that ensure that monitoring, maintenance and repair are carried out at the right time. This also involves scheduling and assigning technicians, as well as ordering and stocking the necessary spare parts.
Ideally, this data is created, posted and archived directly in the ERP system. It gives your team direct access to data on all production equipment, labor costs and spare parts, meaning that even maintenance budgets can be accurately planned. At the same time, production planners can see all the company’s machines and production facilities, all maintenance orders and their deadlines within the plant structure.
Keywords
More similar blogposts:
Found what you were looking for?
Start your intelligent search now