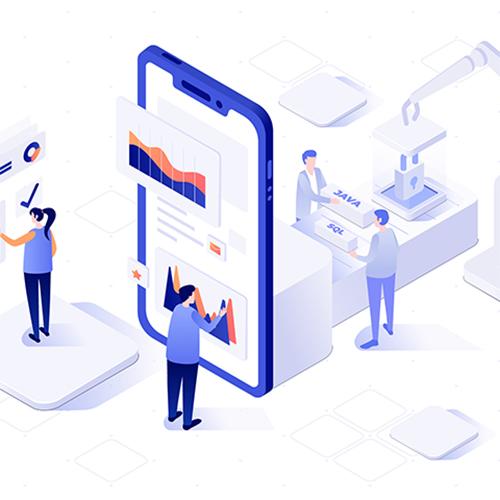
Imagine you could check the status of your machines by pressing a button, or you could view your products digitally throughout the entire value chain. Let's go one step further: you can eliminate errors before they even occur. These scenarios are now reality thanks to the ability to map the entire product life cycle.
Everything at a glance
what do we mean by “end-to-end”? In this context, we mean that products can be digitally mapped out in their entirety from conception to sale. So you can continuously track their entire life cycle.
To date, this has not been possible without using complex solutions that are a pain to work with and require a whole range of different and disconnected systems. Optimum product lifecycle management should not require media disruptions, it should be centrally manageable and operable on different devices. In the digital era, we should be able to collaborate on tasks and access important documents from anywhere.
ERP is the heart of the system topography
An big key element in this approach is the ERP system. But the ERP system can't fulfill the requirements mentioned above all on its own. What it takes is seamless interplay with additional components. It’s not a good idea to think of ERP systems as multi-tools and try to cram as many functions and tasks into them as possible. The goal should be to seamlessly interconnect software and systems in the course of digitalization. In other words, the different components (ERP, CRM, data & analytics, modern workplace, ...) should join up to form an efficient overall system.
In short:
The transitional path from the classic ERP system to the individual solution platform.
Predictive maintenance
The second key factor for such end-to-end scenarios is predictive maintenance. Malfunctions in machines, equipment and systems can come up at any time and create expenses due to production downtimes and downstream repairs. But what if you could predict them ahead of time? What if you could know today which part would fail tomorrow? In predictive maintenance, critical machine components are equipped with sensors that continuously transmit data. This plethora of information is filtered for relevant values, formatted as necessary and can then be used to draw conclusions about the status of a machine. This allows us to predict when critical threshold values will be exceeded, potentially resulting in failure. Information can be prepared as a graphical analysis and displayed on smartphones or tablets. This way, you know how your machine is doing at any time. So you can schedule maintenance well in advance and not be caught off guard by malfunctions at inopportune moments.
Services utilizing augmented reality
Keyword maintenance: Predictive maintenance lets you predict when you’ll need maintenance work and time it accordingly. But now there’s also a way to make repairs faster, cheaper and more efficient than ever – augmented reality. When a problem occurs – or rather, when an impending failure is identified – the service rep performs the maintenance work on site with spare parts and a set of VR glasses. The technician is linked up with an expert at the head office who is familiar with the fault and prompts him accordingly. This saves the company resources and money, since one expert can assist multiple service technicians who perform maintenance work under his instructions. Thus, we can guarantee a seamless maintenance cycle – thanks to predictive maintenance and augmented reality.
Conclusion
Nowadays, a product’s entire value creation chain can be described and represented digitally. From production to intelligent monitoring during installation and down the line to predictive maintenance. Long gone are the days when such end-to-end scenarios sounded like science fiction. Here at COSMO CONSULT, we can help you get there, too, and bring your product lifecycle management to the next level!
Keywords
More similar blogposts:
Found what you were looking for?
Start your intelligent search now