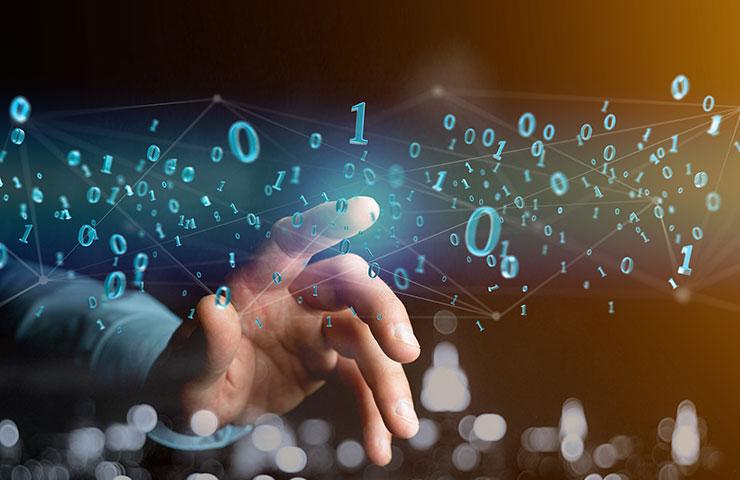
In times of crisis, companies are more keen than ever to find ways to spare resources and do business more efficiently. Just as with the financial crisis of 2008, we’re seeing more interest in digitalization and process automation. We're going to tell you how companies can use forecasting and optimization functionalities to navigate safely through the corona crisis.
Businesses in a state of emergency
“The way we’ve always done it” isn't quite working. Listening to your gut isn’t the best way to make decisions right now either. For example, many companies have their trusted ‘old-timers’ who know just when to restock which materials or products. “Normally, I’d be ordering raw materials about now. Making sure production is set for the next few weeks. But 37% of my business volume has just been wiped out.” – How do you decide in this situation? Tie up capital during the crisis and risk a liquidity squeeze due to high order volumes? Scale back investments and prepare to face a production stop? Is it really the right time for this order? Did we figure out the right quantities to restock? Did we get a good price and secure the best possible terms for delivery? – These are questions that a lot of companies now find themselves struggling to answer.
Help with difficult decisions
In a situation for which we have no real empirical data, where changes can happen from one day to the next and supply chains are no longer reliable, you need tools with decision-making intelligence. COSMO CONSULT combines ERP systems with online-service capabilities for mathematical forecasting and optimization. For example, you can use article, supplier and inventory information to optimize order proposals in the ERP – order the right items in the right quantities at the right time and from the right supplier. The idea is to make business solutions more intelligent, so that users can make better decisions, make more accurate plans for the future and streamline their processes.
Don't be afraid of your own data
The complexity of working with copious amounts of data can often be overwhelming for users. For instance, when it comes to producing data for planning purposes or other material management decisions in a short amount of time. This problem is exacerbated when the decisions involve multiple plants or even the entire supply chain. Luckily, online forecasting and optimization services can help. Not only do they make it easier to collect data – they also provide scalable processing power, all while reducing internal costs. Intelligent assistants provide the information you need in order to make decisions.
Your ERP can learn to do much more!
For example, an intelligent assistant can use daily processing differences to determine the effect on stock, capacity or quality. What’s more, it can even use this data to make recommendations for action and trigger a service order in the ERP system, for example. These kinds of decisions go well beyond the usual “if then” logic in the ERP system. Intelligent assistants are able to assess recurring patterns and “learn” to make better decisions in the future. So tolerances are no longer static – they adapt dynamically to each situation.
The outlook for SMEs
One more crucial detail... Small and medium-sized companies in particular will be glad to know that, as online services, intelligent assistants can be easily integrated into an existing ERP system using a connector. The plug & play principle gets priority. The idea is to provide intelligent functionality without too much effort and produce results for the company in a short amount of time.
Keywords
More similar blogposts:
Found what you were looking for?
Start your intelligent search now