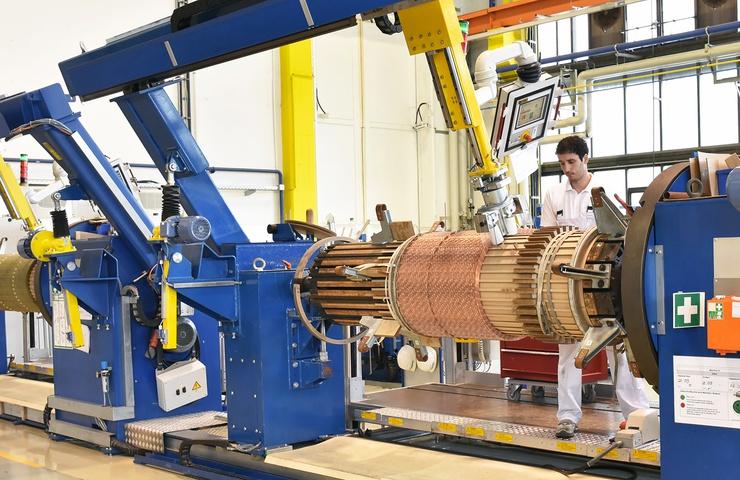
Industrial companies rarely produce products in one work step. Most of the time, a number of operations is required to complete a product. These operations can be summarised in a work plan, and processed successively in a production order. Materials can be removed and posted to the operation for each individual operation. Equally, working times of employees can be reported for the operation.
The costs of this material and the labour time reported are ascribed to the production order and thus to the final product with each operation. It is called work in progress (WiP) if the value of the production order increases.
Determination of profitability
Work is performed and time and material are reported until the final product is completed and all costs of production have been posted. Now, the access of the product to the warehouse, with the costs according to the selected valuation method (moving average, standard costs or actual costs, etc.), can be posted, or a value already posted can be corrected.
Now, the planned costs of preliminary costing can be compared to the actual costs of final costing, and the profitability of the order can be determined. This means that up to the feedback from the final product in the production order, no stock item entry of the finished product has been effected. All costs are just considered work in progress (WiP) and can only be posted as a value in order to be visible. Transfers, stock-taking, assignment to other production orders (e.g., due to rework), etc. are thus impossible.
Operations are often not reported individually, or material is not counted upon actual consumption but according to the default value of the parts list. In the first case, this is called inline production, in the second case backflushing (target = actual). But in any case, the costs of production are posted upon completion of the production order, and thus become visible at the product.
Declaring individual operations as separate assemblies
In many cases it is necessary or desirable to post the individual operations before finishing the final product as a separate assembly and therefore as a genuine part. These semi-finished products are created and posted with separate production orders. Similar to the final product, the assembly is in stock with the value according to the valuation method. Transfers, stock inquiries or even a sale of the semi-finished product are possible. For this assembly production to be mapped in the ERP system, you must create a separate part (the assembly) with a separate work plan and a separate parts list. A separate production order must be created for production. The effort is proportionate to the benefit of the separate treatment possibility of the semi-finished product.
Semi-finished products and finished products in the print & packaging industry
The print and packaging industry requires semi-finished and finished products. After each operation, a semi-finished product shall be laid in stock, and yet the finished product shall be produced in one operation with several operations. This is not possible using the standard tools of an ERP system. A solution for the print and packaging industry therefore needs special functions which can cover these requirements. One solution is the automatic generation of semi-finished products and the modification of the parts list of the production order. That is precisely what the WiP function of COSMO CONSULT´s Print and packaging does.
According to preset parameters (WiP group), the system automatically generates semi-finished products and saves them as parts in the parts master data. These are specifically generated for the respective production order and marked as such (WiP parts). What is decisive is the identification of the operation in which they are produced. These parts are hence genuine semi-finished products with all the features of genuine parts. The system automatically includes these semi-finished products in the parts list of the production order. First, for them to be created upon feedback regarding the operation and to be posted to stock, and second, to be consumed again in the following operation. This simple method allows the use from both worlds. On the one hand, you can create real assemblies within a production order, post, move, count, label and evaluate them. On the other hand, there is no additional effort for the generation of these additional assemblies, parts, parts lists and work plans. By including the WiP groups, the ERP system is able to perform all of this automatically and independently.
Example
Finally, we would like to explain these functions using an example: Production of a folding box (FB) in 3 operations (10 printing, 20 punching, 30 gluing). The system generates two WiP parts: FB10 and FB20 and a parts list which is linked to the work plan.
- Operation: 10 printing – parts list: create FB10
- Operation: 20 punching – parts list: consume FB10 and create FB20
- Operation: 30 gluing – parts list: consume FB20 and create FB30
This allows companies in the print and packaging industry to realize the full potential of their ERP system at all levels of production without unreasonable effort when creating parts. This way, you establish much more transparency in the validation of work in progress.
Industry solutions available
Find pout more about COSMO CONSULT´s industry solution for the printing and packaging industry.
Keywords
More similar blogposts:
Found what you were looking for?
Start your intelligent search now