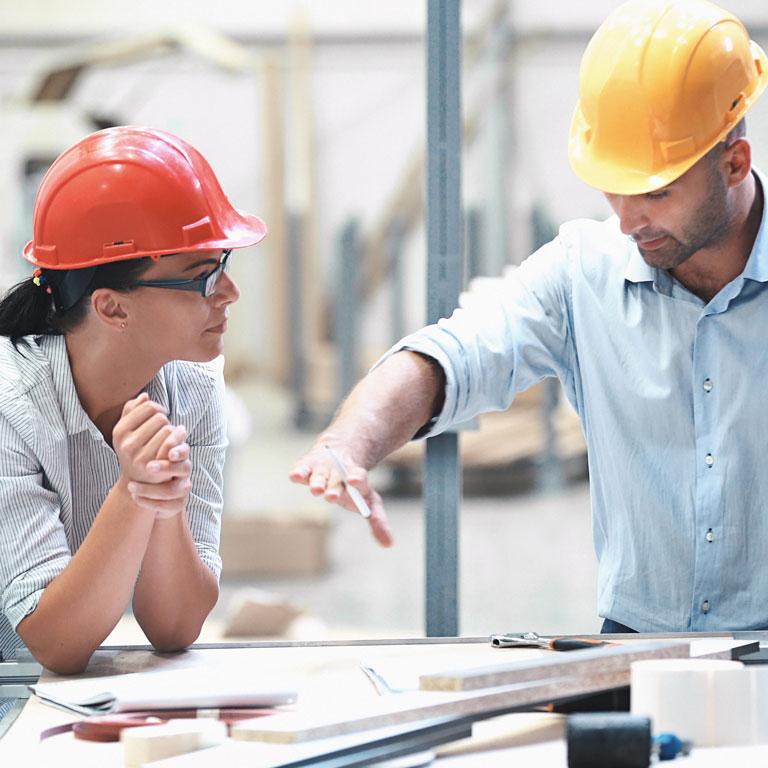
Lately, we’re seeing some increasingly complex and dynamic projects come up. At the same time, the number of project participants is also climbing steadily. All this requires well-structured project planning right from the outset, and that takes professional software tools to control.
In this post, we’ll be giving you a closer look at the individual elements that make up IT-based project planning.
- The project structure plan
- Profit planning
- Process and schedule planning
- Resource and capacity planning
- Project controlling
The project structure plan
By definition, a project is something unique. But that doesn’t mean that every project structure plan has to be invented from scratch – at least not as far as the basic structure is concerned. All it takes is some project templates. Working with project templates also ensures that the project portfolio can be easily analyzed and evaluated – say, using a BI tool.
What makes a project so unique starts right from the project BOMs for machinery and plant manufacture, as well as the individual assemblies in the project structure plan. BOMs can be compiled using master BOMs and individual articles from the article master, which, ideally, should also fulfill the prerequisites for profit planning: purchasing terms and delivered prices.
Profit planning
Using company resources like articles or services, profit planning can be generated almost automatically from the project structure plan. The expected revenues and profit margins are calculated using the traditional overhead calculation method with or without a costing sheet and surcharges for the various pricing groups. Based on the budget plan, you can
- calculate project quotes
- set up project controlling and
- invoice projects.
Project planners and project controllers no longer have to worry about hourly rates or purchase prices. One exception, however, is special purchased or externally produced parts which require requesting individual pricing based on the project. Thanks to our integrated solution, your staff can send requests to Purchasing straight from the project without the usual effort of checking and coordinating.
Process and schedule planning
In addition to cost and profit planning, process and schedule planning can also greatly contribute to the success of your project. First, the individual planning processes are derived from the project structure. These processes are subsequently used as a basis for defining the various process steps and how long they should take. These steps can then be linked up through relationships to predecessors. This way, they can be controlled and and re-scheduled with restrictions. First of all, you have to determine if you’re going to schedule by the earliest or the latest time, i.e. from the start date onwards or from the end date backwards. Milestones make schedule management even more effective and are then used as the basis for project accounting.
Resource and capacity planning
Every resource has a certain capacity, depending on the given work time model. The available capacity forms the basis for resource planning. The main question is this: which resource is scheduled for which project, to what extent and for which time period? The only way to get an accurate answer is to thoroughly plan out your resources. Just don't forget that day-to-day operations generally continue alongside project work, and absences for things like vacations or training also need to be considered. So the capacity actually available for project work might be quite a bit lower.
Our industry solution cc|project lets you see at a glance if a worker is overbooked or still has available capacity.
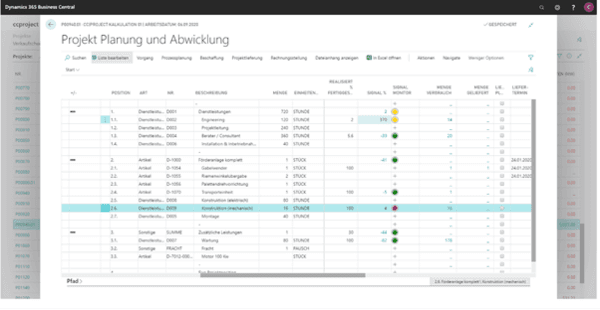
Project controlling
Want to know the costs accrued so far and how much is left of your budget? How about getting that info for each individual assembly? No problem. With integrated project planning, all costs are posted directly to the project – whether it’s the work hours of the project team members, purchasing invoices or travel expense reports. As soon as it’s posted, the information is then available for further analysis. That means that your staff can access the latest figures from any detail level. You’ll know early on how much cost you’ve accrued and whether or not the budget will suffice, in relation to the overall project or a specific plant, assembly and even for individual purchased parts or scheduled work packages.
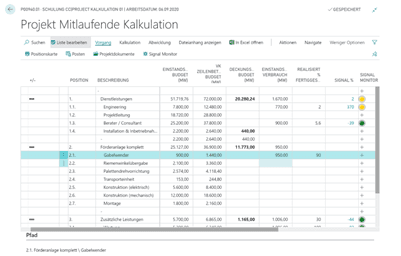
This lets project leaders to identify deviations early, take countermeasures and log the information in the project status report.
Keywords
More similar blogposts:
Found what you were looking for?
Start your intelligent search now