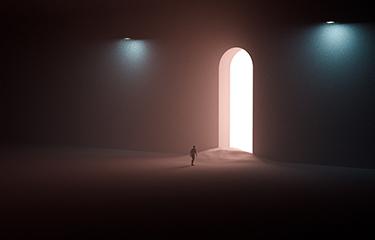
Den digitala utvecklingen inom tillverkningsindustrin går just nu mycket snabbare än i de flesta andra branscher. ”Tillverkningsindustrin svarar för nästan 20 procent av näringslivets förädlingsvärde som räknas in i bruttonationalprodukten, BNP. Industriproduktionen utgör därmed en mycket viktig del av svensk ekonomi.”[1] Det är inte minst därför många avancerade system som utvecklas i Sverige har sin utgångspunkt i tillverkningsindustrin. Det händer så mycket att utvecklingen kallas för den fjärde industriella revolutionen. Och det finns många starka drivkrafter bakom det här. När digital teknik, Internet of Things (IoT), Artificiell intelligens (AI) och smart datahantering samverkar leder det till en högre grad av automatisering, bättre produktkvalitet och att det går att producera specialbeställda varor snabbare och enklare. Det leder i sin tur till effektiviseringar, kostnadsbesparingar och inte minst nya affärsmodeller och tjänster. Det är därför inte förvånande att den svenska tillverkningsindustrin är i hög utsträckning redan automatiserad.[2]
Vad innebär den här digitala transformationen i praktiken? Hur används uppkopplade produkter, automatisering och dataanalys rent konkret för att utveckla produktionen? Och vilka verktyg behövs för att digitalisera tillverkningen? Vi ska titta på några exempel från verkligheten.
Hur ser digital tillverkning ut i praktiken?
Inom tillverkningsindustrin handlar digitaliseringen till stor del om att koppla upp och koppla ihop inte bara den tillverkande utrustningen utan även de medarbetare som är involverade i tillverkningsprocessen, och även kunderna. Med moderna system som hanterar tillverkningsprocesserna och smarta uppkopplade sensorer som förmedlar data för analys går det att utveckla produktionen. Det här för med sig fördelar som:
- Det blir lättare att möta kundernas unika krav. Modern tillverkning går alltmer mot att bli kundorderstyrd och anpassad. Med digitala lösningar som en produktkonfigurator på hemsidan som visar vilka alternativ som går att tillverka och till vilket pris blir det som kunde vara en komplex process både snabb och enkel.
- Smartare tillverkning och förebyggande underhåll. Att ha uppkopplad utrustning i produktionskedjan (sensorer, kameror, mm skickar konstant data) gör att det går att hitta och åtgärda felaktigheter och flaskhalsar m.m. för att få en mer effektiv tillverkning. Att avvikelser i maskinerna går att upptäcka och analyseras leder till att det går att utföra underhåll innan det uppstår problem.
- Bättre support och kundupplevelse. Uppkopplade produkter kan övervakas efter leverans. Det leder till att det går att gå in med underhåll innan det uppstår problem hos kunden. Det blir också lättare att erbjuda tilläggstjänster som ger mer värde för att man har ett bättre dataunderlag.
- Snabbare och bättre design. Att arbeta med digitala produktdesignmodeller i en virtuell miljö är dels tids- och kostnadseffektivt. Men framför allt så går det att gå från idé till färdigtestad produkt mycket snabbare. I produktutvecklingsfasen kan till exempel många tillverkningssteg för en början simuleras på datorn.
Med dessa exempel har vi bara börjat att skrapa på ytan vad det gäller digital transformation för tillverkningsindustrin. Det dyker upp nya verktyg och möjligheter hela tiden, och de mest framgångsrika tillverkarna är inte sena med att ta till vara på dem. Vi ska titta på några exempel ur verkligheten.
Förbättrad kvalitet och energieffektivitet med IoT
PUCO (Pulver-Color Beschichtungs-Ges.m.b.H.) är ett österrikiskt företag som utför standardbeläggning av industriprodukter samt även kan belägga enskilda specialprodukter i stora eller små partier. Bland kunderna finns fordonsleverantörer och flygplanstillverkare. PUCO har valt att samarbeta med COSMO och introducera Microsoft Dynamics 365 som nytt affärssystem för att få en smartare ERP-lösning som gör produktionsprocesserna mer effektiva och flexibla. PUCO ville börja använda sig av IoT och behövde en plattform för den digitala transformationen.
Mjukvaran implementerades av COSMO CONSULT, och utifrån PUCO:s behov av att kunna avgöra i exakt vilket skede av processen en viss beställning befann sig utvecklade sig det hela till ett IoT-projekt. Lösningen för den här utmaningen blev att sätta in RFID-transpondrar i de objekt som rullar igenom driftsprocessen. Med transpondrarna kopplade till en specifik order på mjukvarusidan kan PUCO få full insikt i vad som händer i produktionen och vilka resurser som används. Det här har lett till ett mycket bättre utnyttjande av kapaciteten och PUCO kan nu ta på sig ytterligare beställningar. Vilket har lett till en betydlig försäljningsökning.
Ytterligare en vinst med projektet är att kvalitetssäkringen har förbättrats eftersom det nu är lättare att analysera parametrar som råvaror, temperaturer och eldningstider. Dessutom upptäcktes en optimeringspotential: Varje ugn laddas med en cykel på 20 minuter för att säkerställa att pulverlacken värms upp tillräckligt länge. Kommer ett objekt till ugnen sent riskerar det att antingen hamna under minsta bränntiden eller att tvingas vänta till nästa laddning. Tack vare IoT-datan från lösningen har det gått att eliminera den här flaskhalsen.
Bättre transparens och global samordning
VirtaMed utvecklar simulatorer för endoskopi och kirurgiska ingrepp inom bland annat ortopedi och urologi. VirtaMed:s teknik hjälper till att förbättra utbildningskvaliteten för läkare och effektiviteten av kirurgiska ingrepp utan behovet av att öva på levande patienter. Som de flesta framgångsrika företag växte VirtaMed snart ur sin startup-kostym. Antalet dokument och fakturor ökade och det fanns ingen gemensam databas. Med mer administration och ökade kostnader som följd. För att göra det lättare att spåra processer och att analysera affärssiffror valde VirtaMed att samarbeta med COSMO CONSULT för att implementera Microsofts Dynamics 365 ERP-lösning.
Det här samarbetet ledde inte bara till effektivare affärsprocesser. VirtaMed tillverkar på beställning och många av produkterna är individuellt anpassade efter kundens behov och krav. För att göra produktionsplaneringen mer flexibel valde projektgruppen att komplettera affärssystemet med COSMO:s egna industrilösning för kundorderstyrd tillverkning. Tack vare den går det nu att säkerställa att det alltid finns tillräckligt med material tillgängligt för att utföra beställningarna i tid utan att ha ett för stort lager. Dessutom kan VirtaMed göra ändringar i praktiskt taget varje steg i produktionsprocessen. Via avancerad serienummerspårning kan de installerade komponenterna identifieras och det går att bestämma den exakta konfigurationen av varje simulator. Med den här informationen kan VirtaMed ge sina kunder bästa möjliga råd och support.
Med sitt nya affärssystem har VirtaMed inte bara optimerat sina nuvarande processer utan har även satt kursen mot framtiden. Tack vare den flexibla, öppna tekniken kan nya applikationer och molntjänster enkelt integreras med lösningen. Med bolag i både Zürich och Florida går det också att synkronisera systemen och säkerställa att bolagen arbetar med samma stamdata -från vilken plats som helst.
Snabbare processer och möjligheten att optimera produktionen
Tyska Ackermann Gmbh:s tjänster fokuserar på butik, utställning och inredning, komponentenheter och produktutveckling samt arkitektur och konstföremål. Deras gamla IT-lösning hade blivit alldeles för statisk för den här individuella tillverkaren. Företaget behövde ett dynamiskt system där det var möjligt att göra användarspecifika förändringar i de komplexa och individuella beställningarna. Ackermann hittade vad de behövde i Microsoft Dynamics 365. En branschlösning som gick att anpassa individuellt till Ackermanns processer. Dessutom mötte systemet kravet på en lösning för produktdatainsamling (PDA).
Efter ett möte med COSMO CONSULT insåg Ackermann att COSMOs egenutvecklade lösningar COSMO business och time data acquisition riktade sig speciellt mot just de punkter som Ackermann arbetat med så länge. Tidigare behövde de anställda fylla i dagliga arbetsrapporter som sedan fördes in manuellt i IT-lösningen. En långsam process som kunde ta dagar. Nu loggar de anställda in med sitt personalnummer och projektkoden och all data går automatiskt in och hålls uppdaterad i varje projekt. PDA-resursen ser i sin tur till så att det finns underlag för efterkalkyl. Något som är mycket viktigt för att kunna optimera framtida processer. Det här har lett till en mycket effektivare produktion, samtidigt som det går att ge kunderna snabba och tydliga besked både under och efter tillverkningen.
Rätt verktyg för den digitala transformationen
Som vi ser så öppnar digitaliseringen av tillverkningsindustrin upp enorma möjligheter, och det här är bara början. Det kommer att dyka upp fler innovativa och effektiva lösningar som förbättrar såväl tillverkningsprocesser och kundservice som att de erbjuder nya lönsamma affärsmodeller. Det viktiga är att ha förutsättningarna för den digitala transformationen.
Det moderna affärssystemet utgör själva grunden för att automatisera, effektivisera och knyta ihop digitala lösningar. Microsoft Dynamics 365 Business Central är skapat just för att erbjuda ett komplett utbud av funktioner och en stabil grund för digitaliseringen i din verksamhet. Dessutom har vi på COSMO utvecklat lösningarna just för tillverkningsindustrin som ger mer kontroll och fler möjligheter i den digitala transformationen.
Vill du veta mer om hur ditt företag kan ta steget in i den nya industriella revolutionen, ta bara kontakt med oss så berättar vi mer om alla nya möjligheter.
Nyckelord
Fler liknande blogginlägg:
Hittade du vad du letade efter?
Starta din intelligenta sökning nu